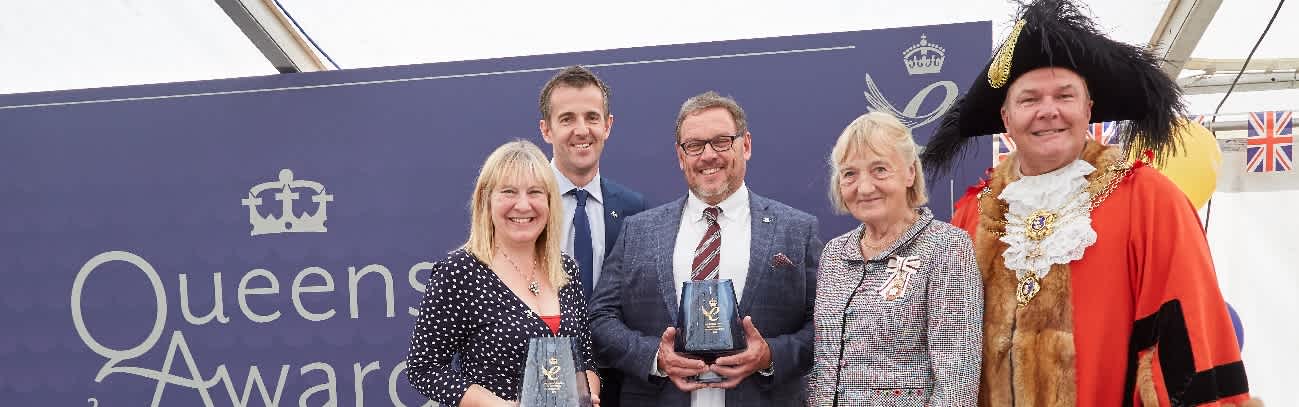
In an Ideal world...
As the only boiler manufacturer globally to be certified to ISO 50001 for its energy management with BSI (British Standards Institution), the environment is always a top priority. Here’s what we’re doing to try and make a difference:
Energy
Improving energy efficiency has been a focus across all departments. Test rigs in the Research & Development labs have been modified with modulating pumps, solenoids and real time monitoring, all which reduce the gas and water consumption of these rigs. On the assembly lines, the number of domestic boilers which are now dry tested increased by 254% in 2017, against a target of 20% increase. 2019 will see the advancement towards 100% dry testing on all domestic boiler models. The savings of gas and water have therefore been phenomenal. Dry testing, plus fast-acting roller shutter doors, a new efficient warm air heating system for the factory, reduction of the oven curing temperatures by 10ºC following an efficiency trial, and the optimisation of building use on site have all contributed towards reductions in gas consumption since 2012 of 3.7 million kWh, a 26% reduction.
LED lamps continue to be installed across the site and is now a standard achieved when any lamps require replacement. Replacement of the compressor with a more energy efficient model, reduced onsite electricity consumption in 2015 by 900,000kw. Because of these types of projects, along with staff behavioral change to adopt a “switch off” ethos, electricity consumption has reduced across the site since 2012 by a staggering 2.6 million kWh, a 38% reduction.
The focus on improving energy efficiency has also resulted in a 40% reduction in the tonnes of carbon emissions associated with energy consumption at the Hull site, since 2012. This equates to 2,496 tonnes of carbon saved. Savings are likely to continue into 2019 with the £1.19 million investment in a new paint line with heat recovery and increased line speed for optimum efficiency.
Waste
As the company has grown, waste volumes have decreased year-on-year. For example, in 2018 a 7.8% reduction in general waste was achieved, and a 4.6% reduction in all waste streams, including recyclables, when measured against company turnover. Over recent years, Ideal have achieved, and continue to maintain “zero waste to landfill” for all general waste streams. Importantly, no single-use or product-related plastics from the site are sent to landfill.
Waste project achievements have been numerous. Highlights include:
Food waste from the canteen is separated at source and sent to a local AD plant, generating biogas to feed into the gas grid.
Reuse of 7200 bricks from the demolition of an internal wall during site re-development.
Finally, all packaging used to pack wall mounted and floor standing boilers is 100% recyclable, supporting our customers with their own recycling targets.
Resources
Resource savings have been targeted across the company. All cardboard used in the packaging of Ideal boilers is made from at least 70% recycled content and has been sourced sustainably. One of the biggest achievements in this area is the work done with major suppliers to encourage use of returnable packaging. 11 high volume suppliers now send Ideal parts in returnable packaging, contributing to the waste reductions on site. Secondary benefits were also realised in optimising the number of products per pallet. For example, Kromschroder components now arrive 568 per pallet, whereas previously only 260 per pallet was achieved. This reduces transport impacts associated with diesel emissions and fuel consumption for our suppliers.
Ideal have kept pace with improved engine efficiencies for light commercial vehicles, replacing the fleet on a rolling programme until all will achieve Euro 6 Standard in 2019.